Trust the Process
At Keldin we are committed to achieving the highest standards of quality and delivering it right first time. We hold ISO 9001, ISO 14001, and ISO 45001 certifications. To achieve our high standards, we apply a strict and proven quality assurance process to every project:
Step 1: Workshopping
Once we are awarded a contract, we hold a quality workshop to review the requirements and identify the key elements that will determine the success of the project. By focusing on these elements, we ensure the delivery of a quality product that meets, and where possible, exceeds the expectations of our clients. Our ‘Zero Snags, Zero Defects’ approach informs the ethos of the Keldin team.
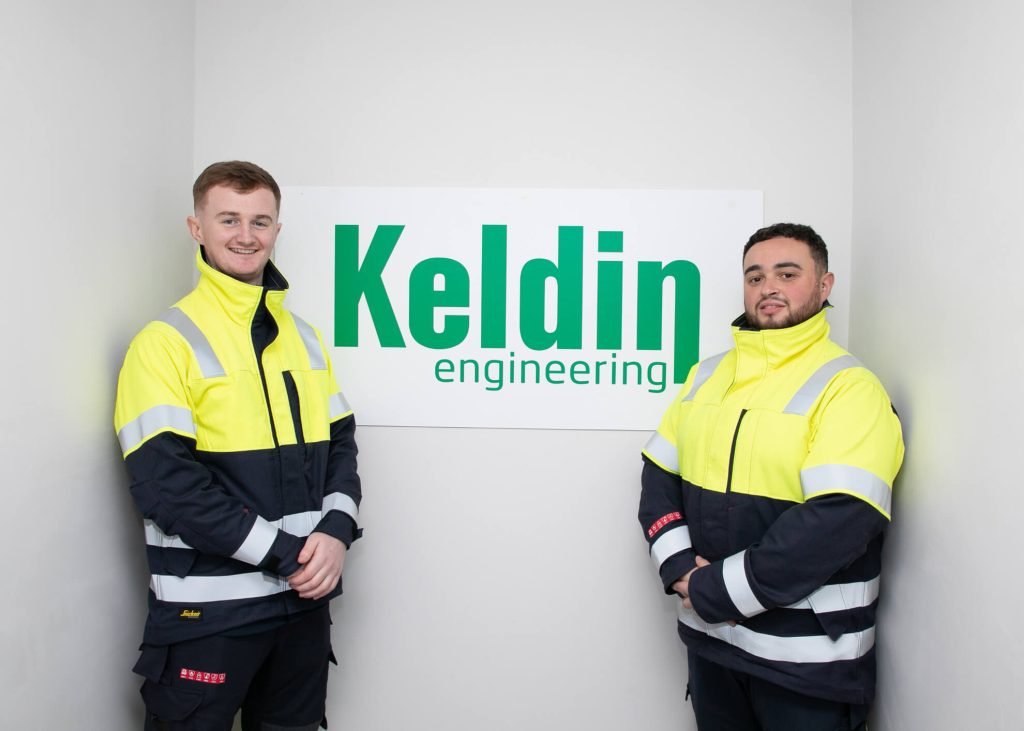
Step 3: QA Check Sheets
QA Check Sheets form the frontline inspection and ensure that the installed product is built correctly and is ready for the Installation of the Ext trade’s work. The Check Sheets are bespoke for each project and are written on the back of the work done in the Test and Inspection Plan.
QA Sheets are prepared to be used as checklists on site – condensing all the knowledge gained on the project and previous experience into a workable A4 tick sheet. These Sheets are then passed on to the specialist contractor, who checks their works and ensures that the area is clean and tidy before handing over to our Site Managers. During the early builds and processes and once the Site Managers have inspected and accepted the works offered, we give the client team the option to inspect. Once all interested parties are happy that the area of work has been installed to the agreed tolerances, and built correctly to the specification, we issue a handover document to the trade following on and they are able to commence work.
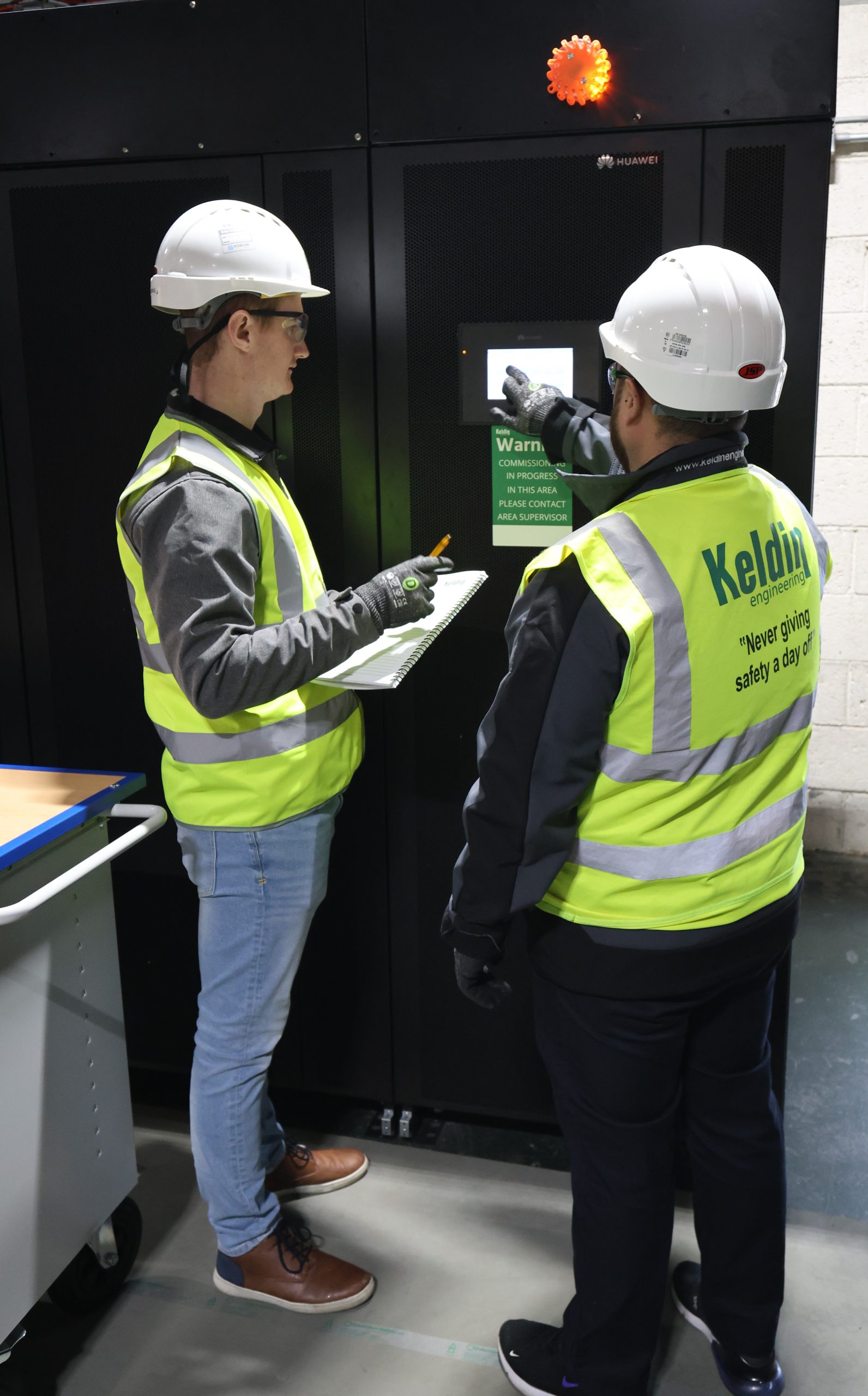